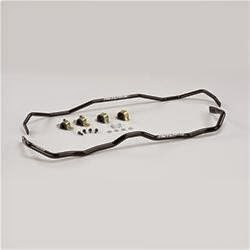
AUDI TT Sport Sway Bar Kit 22806 - Installation of Hotchkis Front Sway Bar 1F Raising Vehicle Raise front of the vehicle by using a 4 post lift or drive-on ramps. Securely block the rear wheels of the vehicle. Do not remove the front wheels during installation for safety. 2F Observe Orientation Of the Bar Remove the lower splash shield, and observe the location and orientation of the front swaybar. 3F Remove End Links Locate and remove the lower end link nuts
from both sides, and push links aside. 4F Remove Engine Mount Locate
and remove lower engine mount that attaches to subframe.
The engine may
want to shift forward which is ok. 5F Remove Exhaust Hanger
Use a pry bar to remove the exhaust hanger located behind subframe. 6F
Ride...